Rundgang durch die historische Schleifmühle
Der virtuelle Rundgang führt uns durch die historische Schleifmühle Asbacher Hütte und durch die Wetzsteinschleifhütten des Unterammergau.
Schleifmühlen sind nicht selten und oft findet man diese direkt in den Hammermühlen in Form diverser Schleifsteine, oder man baute extra eine eigene Schleifmühle nur wenig entfernt der Hammerwerke.
Dabei wurden hier die in den Hammermühlengefertigten Metallstücke beschliffen oder poliert. Gerade in den Klingenwerkst&ätten von Solingen findet man dann viele sogenannte Schleifkotten, welches dann wasserbetriebene Schleifmühlen waren. Doch nicht nur Metall wurde geschliffen und poliert, auch Mineralien und Gesteine. Hier wurden Edelsteine für Schmuck und Zierde beschliffen, oder aber es wurden Steine zu Bodenplatten, Wandkacheln oder Werkstücken beschliffen.
Wir werden daher hier die Edelsteinschleiferei Asbacher Hütte nahe des Edelstein-Zentrums Idar Oberstein vorstellen, aber auch die historische Wetzsteinschleiferei des Unterammergau soll hier vorgestellt werden.
Die Historische Edelsteinschleiferei Asbacher Hütte
Idar Oberstein ist bekannt als Zentrum des Edelsteinhandels. Schon von Alters her wurden hier Schmuck- und Edelsteine geliefert, begutachtet und weiter verkauft. Doch auch die Höhenzüge des Hunsrück boten natürliche Vorkommen von Jaspis, Achaten und anderen Quarzen, so daß sich schon Früh Menschen am Idarbach dessen Kraft zu Nutze machten, um Schleifmühlen zu betreiben. So findet man auch in Idar Oberstein im dortigen Edelsteinmuseum eine Schleifmühle, aber auch am Idarbach hat die historische Weiherschleife "überlebt", wobei man hier sagen muss - mag das Gebäude historische Wurzeln haben, so ist das Wasserrad eher ein Kunstobjekt und die Schleifmühle wirkt auch nicht historisch.
Anders wenige Kilometer nördlich am Fischbach, wo bei Asbacher Hütte eine wirklich historische Schleifmühle steht. Angetrieben wird diese über ein oberschächtiges Wasserrad und auch das Gebäude selbst ist ein historisches Fachwerkhaus und typischer Bauweise der Gegend. Auch ist der Ort nicht so überlaufen wie das Zentrum in Idar Oberstein selbst.
Ursprünglich war es eine Gipsmühle wo mittels Pochwerk Gips gebrochen wurde und dann auf harten Granitmahlsteinen - so erzählt man sich - der Gips zu feinem Puder für Stuckateure und Mörtel hergestellt wurde. Doch im 19. Jahrhundert wurde dann das Gebäude umgebaut und zu einer Achatschleifmühle umgerüstet.
Das Wasserrad der Asbacher Hütte hat einen Durchmesser von nur 3,5 Metern und ist ein oberschächtiges Wasserrad in Volleisenausführung.
Der Mühlgraben zweigt direkt nach der ehem. Harfenmühle ab und versorgt das Rad mit Wasser aus dem ehem. Staubereich der Harfenmühle mit Wasser, welches über einen natürlich gestalteten M&uumhlgraben das Wasser der Schleifmühle zuführt.
Das Rad ist nur rund 50 cm breit und erbringt daher nicht viel Leistung, dies war aber aufgrund der Schwungmassen im Inneren auch nicht notwendig - denn diese Massen liesen die Mühle gleichmäßig drehen, auch wenn das Wasser mal schwankte.
Zudem sorgt der oberschächtige Betrieb für optimale Nutzung des Gefälles und benötigt daher auch keine besonders große Wassermenge, ein Grund warum man sehr gern diese Räder nutzte. Auch sind diese Räder wenig anfällig für Treibgut, wie Laub und Zweige, die im Frühjahr und Herbst in den waldreichen Regionen häufig waren. So ist der kurze, eiserne Zulaufkähner auch ohne Rechen gehalten und es gibt oberhalb des Kähnerzulaufes dann ein Doppelschütz, welches den Freischuss öffnet, oder ein keinen Stau im Mühlgraben erzeugt, so daß hier der Betrieb der Mühle mit gleichmäßiger Wasserzuführunggewährleistet werden kann.
|
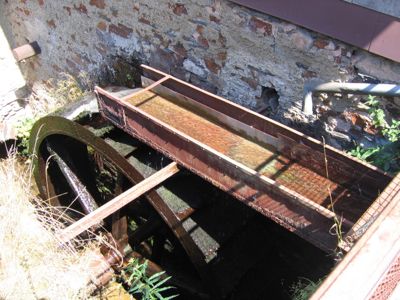 |
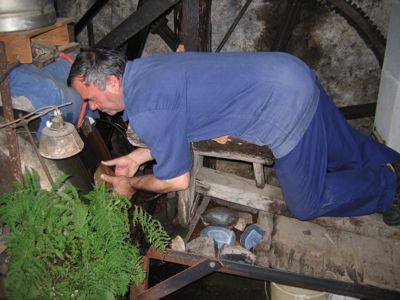 |
Das wichtigste der Edelsteinschleifmühle sind dann die Schleifsteine. Es sind große runde Steine, zumeist Sandsteine verschiedener Härten und Körnungen, welche zum Trennen und Schleifen der Steine benutzt worden sind.
Achate haben eine große Härte und brauchen daher viel Druck, um sicher beschliffen zu werden. Dabei liegen die Steine auf einer langen, fr¨hrer hölzernen Welle, wo diese entsprechend verkeilt worden sind. Heute sind es Metallachsen, die über ein kleines Vorgelege direkt vom Mühlrad angetrieben werden. Oft zweigte man vom hoch liegenden Zulaufkähner dann frisches Wasser ab, um die Steine zu befeuchten und den Schleifstaub abzuspülen.
Andere Steine drehten in einer hölzernen Wanne, wo diese befeuchtet und gereinigt worden sind.
Der Edelsteinschleifer liegt auf einem Langschemel und presst sich mit den Füssen von einer Kante ab, womit er den Schleifschemel fest in Richtung der Schleifsteine. Die unebenen Schnittstellen der Achatdrusen, wie man die Kristallgefüllten Gesteinsblasen nennt, werden so geebnet und nach und nach poliert.
Beim Polieren haben einige Schleifmühlen einen anderen Stein, zum Teil auch Holzscheiben, die dann mit feinem Sand, Tonmineralien, Gips- und Talkumpuder bestrichen werden. Der feine Staub nimmt dann beim Reiben nur ganz wenig Material ab, wodurch die Fläche fein und auf Hochglanz poliert wird. |
Neben den großen Schleifsteinen ist in einer Edelstein-Schleifmühle natürlich auch das Schneiden, Trennen und Polieren sehr wichtig.
In der Asbacher Hütte werden dazu Maschinen vom Wasserrad über Transmissionsriemen angetrieben. Dies sind Diamant besetzte Schleif und Trennscheiben, Schleifsteine aus Quarz oder künstlichem Korund, diverse Poliersteine zum Polieren von kleinen Oberflächen.
Nein, sauber und warm ist es nicht. Der Ort ist eher kühl und feucht, er muss gerade im Winter eine furchtbare Arbeitsstätte gewesen sein, über die ein kleiner Kanonenofen in einer Ecke nicht hinwegtäuschen kann. Selbst wenn man nicht an den Großen Steinen gearbeitet hat, war die Arbeit an den Trenn- und Kleinscheibenwerkzeugen kein Zuckerschlecken. Alles in allem fehlt zumdem Licht, selbst an dem Tag, wo die Aufnahmen entstanden sind, wo es über 30° C im Schatten hatte und die Sonne schien war es in der Mühle eher düster und kühl.
So kann man sich vorstellen, wie wichtig damals Licht war und wie anstrengend die Arbeit wirklich gewesen sein muss, wollte man herausragende Arbeit abliefern, gerade in trüben Herbst- und Frühjahrszeiten war dies an den schnell rotierenden Trennscheiben eine Kunst, wenn nicht Glücksspiel. |
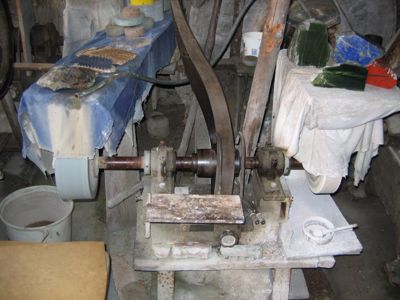 |
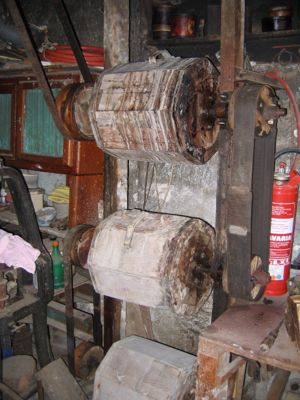 |
An der Rückwand der Mühle drehen sich unablässig die hölzernen Schleiftrommeln.
Wir kennen die kleinen, von allen Seiten rund und glatt polierten Halbedelsteine. Diese werden in diesen Trommeln hergestellt, von der RKaft des Wassers über viele Tage poliert. Die Steine beginnen rauh und grob, werden daher mit groben Stand und wertlosen, aber harten Steinen zusammen in die erste Trommel eingebacht. Unter dem beständigen Drehen schlagen die Steine untereinander die groben Kanten ab, der Sand glättet schon allzu scharfe Kanten ein wenig.
Danach werden die Steine entnommen, der Größe nach sortiert und dann in eine weitere Trommel gelegt, wo nun Quarz, und Granitkies hinzugegeben wird, der nun die Steine beimn Drehen der Trommel weiter glättet.
Erst zum Schluss kommen diese mit Poliersand in nochmals in die Trommel, wo der Sand die Oberfläche glättet und fein bearbeitet, um diese dann nochmals in die Trommel zu stecken, dann mit Talkumpulver und auch einigen Hartholzstückchen oder Walnussschalen, wodurch die Oberflächen der Steine auf Hochglanz poliert werden.
Die Steine werden den Trommeln entnommen, gewaschen, sortiert und dem Verkauf zugeführt. |
Eine Besonderheit war in der Schleifmühle, daß diese schon früh elektrisches Licht hatte.
Über einen Gleichstrom Generator wurde mithilfe der Hauptwelle und einem Transmissionsriemen diese erzeugt, so daß man hier von einem frühzeitigen Wasserkraftwerk reden kann - wenn auch nur zum Eigennutz.
Beeindruckend war, daß immer noch die urspünglichen Kohlefadenlampen in der russgeschwärzten Deckenfassung glimmten. Von Beleuchtung keine Rede, wirklich nicht, es dürfte daher ungefähr so hell gewesen sein, wie ein Kienspan - so nennt man glühende, harzreiche Stäbchen aus dem Holz von Kiefern - trotzdem dürfte man stolz auf die technische Leistung gewesen sein.
die Schleifmühle war daher auch nachts beleuchtet oder an trüben Tagen war eine Orientierung gegeben, mehr als andere Mühlen hatten.
Der Russ im Innenraum kommt zumeist vom Abbrennen zusätzlicher Kerzen beim Arbeiten, die dann mithilfe von Wasserblasen als Arbeitsleuchte benutzt wurden. Die Kerze wurde mit einem kleinen Spiegel hinter dem mit Wasser gefüllten Glasballon gestellt, das Licht wurde so verstärkt und aub einen bestimmten Bereich gebündelt. Anstelle Kerzen waren auch Talglichter, sogenannte &quout;Tranfunzeln", eingesetzt. Auch dürften Rauchgase des alten Ofens ebenfalls für eine Deckenfärbung gesorgt haben, da beim Anheizen oder auch durch leicht undichte Rohre immer etwas Russ des Ofens in die Räume zog... |
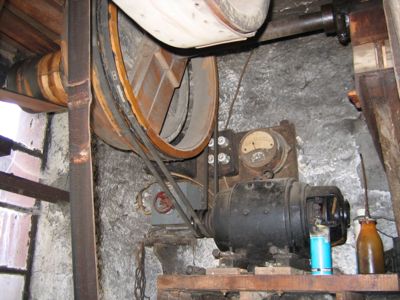 |
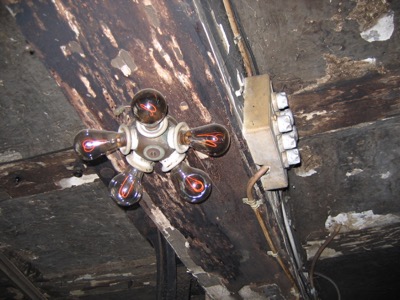 |
Unter der Decke dann, man möchte es kaum glauben: Kohlefaden Glühlampen.
Der Vorgänger moderner Glühlampen, nun seit über 80 Jahren in Betrieb. Der Glaskörper ist mit einem Vakkum gefüllt, in dem ein Glühfaden aus Kohlefasern eingelegt ist. Aufgrund der hohen Temperatur des Stromes beginnt der Kohlefaden zu glühen, kann aber, weil Sauerstoff im Glaskörper fehlt, nicht verbrennen, so daß ein rötliches Glühen erzeugt wird.
Von Licht kann daher keine Rede sein, es ist ein schwaches Glimmen, nicht mehr als ein Kienholz wohl ausgestrahlt haben mag. Trotzdem: Kienhölzer waren eine Brandgefahr und zudem waren diese wertvoll und auch glimmten diese schnell ab, so daß neue Hölzer eingespannt und zum glimmen gebracht werden mussten.
Dies war mit dem elektrischen Glimmfaden der Kohlewendel Lampe nicht mehr nötig. Man drehte den Schalter und die Leuchte glimmte, einfacher und besser als jeder Kienspan - zudem billiger als jede Kerze.
Vielleicht reichte auch hier das Licht nicht aus, um den Raum zu erleuchten, doch zur damaligen Zeit war diese Form des Lichtes purer Luxus. Und da es sich um fünf dieser Lampen handelt, kann man ersehen, wie hell es den Menschen damals vorgekommen sein muss, wenn man für gewöhnlich nur einen Kienspan pro Raum benutzte. |
Um nochmals die Anlagen der Edelsteinschleifmühle oder Achatschleifmühle zu verdeutlichen, hat das Freilichtmusem Hagen die Inneneinrichtung einer solchen Mühle in den Keller eines der Häuser am oberen Marktplatz eingebaut. Regelmäße Vorführungen sollen dieses Handwerk in diesem Industriemuseum zeigen, welches ja letztendlich nahe den Edelsteinrevieren liegt.
Gut zu erkennen ist der große Schleifstein aus Sandstein, mit dem Liegebock zum Schleifen der Steine, aber auch die vielen kleinen Polier- und Trennscheiben, die dann zum Schneiden der Steine und polieren der beschliffenen Flächen dienten.
Zwar ist die Einrichtung mit einem Elektromotor betrieben und auch das Flair einer solchen Schleifhütte kommt nicht wirklich beim Besucher an, trotzdem wird hier der Bau und die Funktion dieser Edelsteinschleifereien deutlich dargestellt, aufgeräumt und hell. Durch die Vorführungen erfährt der Besucher nur zu gut, wie beschwerlich die Arbeit der Edelsteinschleifer war und kann das mühseelige Herstellen von Achtscheiben, polierten Achatdrusen oder Schmucksteinen hautnah erleben.
Wünschenswert wäre ein eher authentischer Ort, doch für das Museum und hier zur klaren Übersicht ist die Sache optimal. |
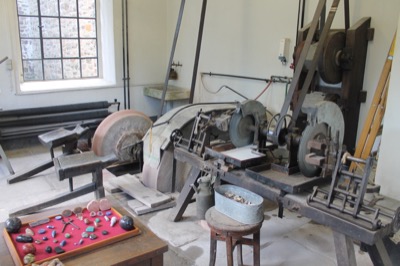 |
Wenden wir uns nun einer ganz anderen geographischen Lage zu und einem nahezu ebenfalls fast völlig vergessenen Handwerk. Der Herstellung von Wetzsteinen.
Wetzsteine waren nahezu in jedem landwirtschaftlichen Betrieb in Gebrauch, alle Sensen, egal ob Langstielige Feldsensen oder kleine Handsicheln, die Schneide musste scharf gehalten werden. Dabei wurde die Schneide von Zeit zu Zeit von einem Schmied oder einer anderen kundigen Person an einem kleinen Metallamboss ´gedengelt´. Mit Hilfe eines Hammers wurde die Schneide auf dem rundlichen Kopf des Amboss wieder dünn ausgeschlagen, das Metall wurde so kalt verformt und wieder zu einer dünnen Schneide nachgeformt, Scharten und Dellen wurden so korrigiert.
Dann kam schon der Wetzstein zum Einsatz und mit geschickten Schwüngen wurde dann die Sense oder Sichel am minalischen Stein geschliffen und somit raisermesser scharf geschliffen. Im Feld hatte jeder der "Schnitter" eine Ledertasche bei sich, in der der Wetzstein griffbereit aufbewahrt wurde. Nach einigen Schwüngen wurde die Sennse abgestellt, kurz mit dem Stein nachgeschliffen und dann wurde weiter geschnitten. Gerade die eher holzigen Triebe des Getreides führten rascher zu stumpfen Sensen, als das weiche, feuchte Gras.
Der Wetzstein war daher ein wichtiges Utensil für die Landwirtschaft und gerade im 19. Jahrhundert ein wichtiges Gut. Fast ein Monopol hatten daher die hochwertigen Wetzsteine aus dem Alpenschiefer des Unterammergau. In dieser Gegend wurde der Schiefer gebrochen, um denn in Schleifmühlen zu den wertvollen und begehrten Wetzsteinen geschliffen zu werden.
Diese Schleifmühlen sind heute verschwunden, indes haben wenige überlebt.
Es gibt zum Einen am Eingang der Schleifmühlklamm im Unterammergau ein kleines Museum, wo ein Nachbau einer Schleifmühle im Garten des Wirtshauses steht. Das Museum kann frei besichtigt werden und zeigt eine neuere Form der Schleifmühle mit rotierenden Schleifsteinen. In der Klamm, die am dem Wirtshaus zu Fuss zu durchwandern ist und in der sich der Schleifbach tosend und wild zu tal stürzt findet man gerade im unteren Bereich eine Vielzahl von Schleifhüttenm, die der Klamm ihren Namen gaben. Meistens sind es nur noch Reste, an einigen kann man aber noch Schleifsteine oder Wasserbauliche Anlagen finden, die deren einzige Verwendung dokumentieren.
Doch dort, wo die Klamm enger wird, der Bach lauter und wilder wird, liegt dann versteckt und in die herrliche Alpenlandschaft wie verwunschen eingebattet die Museumsschleifmühle Unterammergau. Sie wurde nach Originalplänen restauriert und an einigen Tagen ist diese auch für Besucher geöffnet und man kann die mühsame Herstellung der Wetzsteine verfolgen.
Für den Zweck der Darstellung ist der verwinkelte Bau mit seinem versteckten oberschächtiges Wasserrad nicht wirklich geeignet, muss aber hier erwähnt werden. Daher wenden wir uns einer Möglichkeit zu, dieses fast einmalige Handwerk einer Schleifmühle etwas publikumsnäherer Bauweise hier vorzustellen, welches mit der Schleifmühle im Freilichtmuseum an der Glentleiten viel einfacher zu machen ist.
Die Schleifmühle Glentleiten wurde aus dem Unterammergau ins Museum versetzt, da leider viele Teile schon verfallen und zu beschädigt waren, um diese im Museum wieder einzusetzen, wuerden diese nach Erzählungen und alten Bildern restauriert. Ein glücklicher Zufall führte auch einen der letzten Wetzsteinmacher ins Museum, der den Leuten die Arbeitsschritte der Wetzsteinherstellung in Bild und Ton überliefern konnte, so daß ein aussterbendes Handwerk trotzdem durch diese Überliferungen bewahrt werden konnte.
Begeben wir uns daher in die Wetzstein-Schleifmühle im Freilichtmuseum an der Glentleiten.
Das Wasserrad der Wetzsteinschleifhütte im Freilichtmuseum hat einen Durchmesser von nur 3,5 Metern und ist ein oberschächtiges Wasserrad mit Schussgerinne.
Meist wurde das Wasser von einer Gefällestufe oberhalb der Mühle abgezweigt und dann über das Gerinne zugeführt, wobei hier das Gerinne hoch über dem Dachfirst liegt und mit dem steilen letzten Stück auf das Wasserrad geleitet wird. Man versuchte so damals die rasche Wirkung des Wassers auf die Schaufeln zu übertragen, eine irrige Annahme wie man heute weiß.
Der Schusskähner ist zugleich seitlich wie bei den Bauernmühlen verstellbar, so daß Wasser auf das Rad oder an diesem Seitlich vorbei geführt werden kann, um so das Rad in Betrieb zu setzen oder abzuschalten.
Das Rad hat eine Doppelfunktion. Auf dem Wellbaum sitz ein Kammrad zum Antrieb der Schleifsteine und einer kleinen Transmission in der Schleifhütte, zum anderen den Kurbeltrieb. mit dem über die Kuppelstange der oszilierende Wellbaum in der Schleifhütte zum Antrieb der Schneider und Stelzen bewegt wurde.
Im Steilstück des Museums wirkt die Schleifhütte recht authentisch und das deutliche vom Wasser knatternde, rasch drehende Mühlrad ist ein sehr verwunschener Anblick, ein gelungenes Stück Atmosphäre, welches man hier im Museum finden kann... denn genauso kann man sich eine Schleifhütte in der Schleifmühlklamm im Unterammergau vorstellen.
|
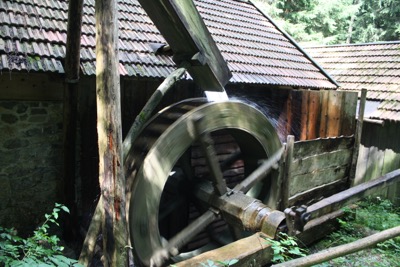 |
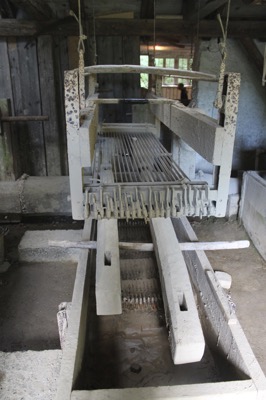 |
Die Steine wurden im Schieferbruch gebrochen und mit Karren oder Kraxen zu Tal gebracht. Dort an den Schleifmühlen wurden die Schieferplatten, Schielen genannt, dann in den Schielenschneider eingelegt.
Auch dort haben wir einen hin- und her schwingenden Rahmen, in dem Bandeisen eingespannt sind. Diese reiben nun über das eingelegte Gestein, welches mit einer Wasserschicht bedeckt ist. Zugesetzter Sand wirkt nun wie Schleifpapier, so daß die Bandeisen sich nach und nach durch den Stein arbeiten und diesen zerteilen. Eine gesonderte Zahnung, wie bei Sägen zu finden, ist durch die Zugabe des Sandes nicht nötig, weil der Sand das abrasive Element zwischen den hin- und her gehenden Bandeisenkanten und der Steinplatten ist.
Die Platten werden so in längliche Stücke geschnitten, die man Stingel nennt. |
Die länglichen Steinstücke wurden dann in einem hinter der Mühle befindlichen Erdkeller, dem Kalter eingelagert.
Dort gab es dann auch eine kleine Hütte, die meist nur einen Hauklotz mit einem kleinen eisernen Amboss, einen Tisch, einen Stuhl und einen Ofen enthielt. Nur wenige der Hütten hatten auch ein Lager, wo der Wetzsteinmacher sich niederlegen konnte.
Im Winter, wenn dann der Frost die Arbeit der Schleifmühlen unmöglich machte, weil die Gewässer zugefroren waren oder Eisgang den Betrieb des Wasserrades verhinderte, wurde der Ofen der Beckhütte angefeuert und der Wetzsteinmacher holte einen Korb der Stingel in die Beckhütte. Mit einem Hammer wurden die Steinstücke nun auf Länge gemacht und das Ende der Steine zugespitzt.
Die Steine wurden so gebeckt, wie man es nannte und die sogenannten Schielen wurden zu "Gebeckten".
Diese Steine wurden dann von der Beckhütte wieder in den Kalter gebracht und eingelagert, die Beckhütte wurde gefegt und der Steinabfall auf Schutthalden entsorgt.
Diese Handarbeit war nötig, damit die mechanische Bearbeitung in den Schleifmühlen nicht zu Zeitaufwendig war, zudem konnte das grobe Behauen der Steine von Hand einfacher als Mechanisch bewirkt werden, ging also schneller. Es war trotzdem in der oft nicht gerade warmen Beckhütte des Winters eine nicht gerade tolle Arbeit, vor allem weil oft bis auf eine Kerze kaum natürliches Licht vorhanden war. |
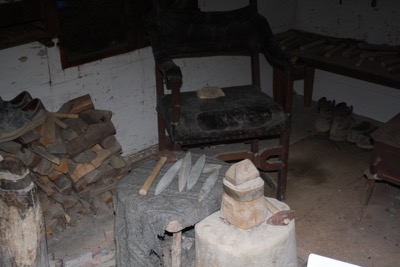 |
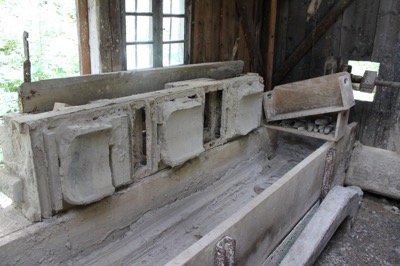 |
Wenn im Frühjahr dann wieder das Eis zurück ging, die Waßerräder wieder in Betrieb genommen werden konnten, wurden die "Gebeckten" in die Mühle gebracht.
Dort kamen diese in die Stelze, so nannte man die Formschleiftröge der Mühle. Auch hier war es ein schwingender Rahmen, der über einen Kurbeltrieb hin und her bewegt wurde. In diesem befand sich ein Formschleifstein. Erneut wurden die Steine am Boden des Trogs eingesetzt, mit Keilen fixiert und dann wurde Waßer und Schleifsand zugesetzt. Man senkte den Schleifrahmen am, der durch sein Eigengewicht und mit Hilfe des Sandes jetzt die Steine im Trog beschliff.
Normale Stelzen hatten hier einen Nachteil, denn diese konnten das Gut nicht so schleifen, wie es nötig war und mußten daher ab und an nachgestellt werden, wobei der Winkel des Schleifrahmens leicht verstellt wurde. Dies änderte sich mit Erfindung der Lehrstelze, die über einen selbst nachstellenden Teil verfügte, die den Schleifrahmen automatisch ein wenig anwinkelte, so daß ein Nachstellen entfallen konnte.
Nachdem eine Seite geschliffen war, wurde der Trog geleert und die Steine wurden mit der ungeschliffenen Seite nach oben erneut eingesetzt, der Trog wieder gefüllt und das Schleifen began abermals. Das Ergebnis waren die "Abgestelzten Steine" oder schlicht "Abgestelzte". |
Nachdem der Schliff der Schleifsteine nun diese in ihre typische Form gebracht hatte, mußte die Dicke noch angepasst werden. Erneut kamen so die Steine in einen Trog, der allerdings wieder einen Rahmen mit Bandeisen hatte, so wurden die breiten, vorgeschliffenen Steine nun auf die korrekte Dicke geschnitten. Das Gerät wurde "Kliebschneider" genannt, wodurch man dann rund 2 cm dicke Wetzsteinrohlinge erhielt.
Damit die Dicke auf wirklich ordentlich und gleich war, wurden die Steine danach meist noch flach in einen Schleiftrog gelegt, der ähnlich der Stelze im beweglichen Schleifrahmen anstelle eines konkaven Granitsteins einen ebenen Stein montiert hatte. Mit Wasser und Schleifsand wurden dann die eingelegten und verkeilten Wetzsteinrohlinge auf endgültige Dicke gebracht. Die nun "Ausgeschliffenen" wie man die fertigen Wetzsteinrohlinge nannte, wurden dann wieder sortiert und eingelagert. |
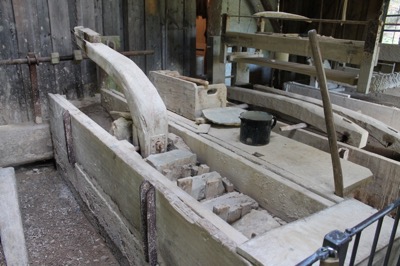 |
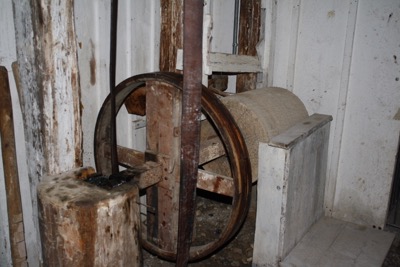 |
Das Ende der Arbeit war das Ausschleifen. Der Rohling wurde dabei an einem drehenden Schleifstein in seine endgültige Form gebracht und die groben Kanten wurden geglättet. Der Schleifmüller preßte dazu den (Wetz-)Stein mit einem langen Holzhebel, den er unter einem Riegel über dem Schleifstein einlegen konnte auf den drehenden Schleifstein. Wasser wurde meist über eine kleine Rinne direkt vom Zulaufgerinne zum Stein befördert und befeuchtete diesen, wusch aber so auch den Schleifstaub vom Stein.
Früher waren dies dann große Sandsteine und Granitsteine, die zum Schleifen benutzt worden sind, im 20. Jahrhundert kamen dann künstliche Schmiergel Schleifscheiben zum Einsatz, die über Transmißionsriemen und Vorgelege auf die entsprechende Drehzahl gebracht wurden.
Die Wetzsteine wurden dann mit Wasser zumeist leicht handschmiegsam gemacht, sprich die Oberfläche leicht anpoliert.
Frauen wuschen dann die Steine mit Wasser, welches es in der Mühle reichlich gab, zum Teil ja direkt vom Waßerzulauf in die Mühle abgezweigt wurde, und entfernten so den letzten Schleifstaub. |
Die fertigen Steine wurden dann in der Mühle oder Lager des Hauses des Schleifmüllers eingelagert.
Später wurden die Wetzsteine dann in groben Säcken, zumeist aus Hanfgewebe ins Tal zu den Genossenschaften gebracht. Deren Häuser, die Steinkästen, hatten ein Lager, wo die Wetzsteinmacher die Steine anlieferten und dann entlohnt wurden.
Im Steinkasten wurde dann aus dem Lager der Wetzstein in Kisten oder Holzfässer verpackt und zum Transport bereit gestellt.
Die Unterammergauer Wetzsteinmacher waren daher nicht ganz eigenständig, sondern mit Genossenschaften schon organisiert und wurden daher schon relativ kontrolliert entlohnt. Eine sehr bekannte Genossenschaft war die "Steinheilgesellschaft", die später zur Bayrischen Mamor-Wetzstein-Genossenschaft umbenannt worden ist.
Deren Namenszug ist noch heute auf alten Wetzsteinen zu finden ist, oder Kisten und Transportfässer ziert. Die Wetzsteine waren ja nicht allein regionales Gut, sondern wurden über den Landweg bis nach Norddeutschland verbracht, zum Teil aber auch mit Lastkähnen, Lastflössen oder später der Eisenbahn in ganz Deutschland auf den Markt gebracht. Doch auch die Alpenanrainer wussten die gute Qualität aus dem Unterammergau zu schätzen, so daß auch nach Österreich, Norditalien, nach Ungarn, in die Tschechei und in die Schweiz geliefert wurde.
Bekannte Namen tauchen in den Handelsbüchern auf, wie Schwäbisch Hall, Chemnitz, Leipzig, Bamberg, Graz, Stuttgart, Nördlingen, Miltenberg oder auch Frankfurt am Main.
Ja, und damit sind wir auch am Ende was Schleifmühlen betrifft. Es gibt zwar noch Schleifmühlen die Mamorplatten geschliffen haben, andere haben Glasschliff gemacht, wieder andere haben Klingen geschliffen und poliert. Noch andere haben in der Rüstungsproduktion Platten und Rüstungsteile für Harnische gefertigt, geätzt und poliert.
Und nicht alle können vorgestellt werden, weil einfach auch die meisten davon heute nicht mehr existieren.
Zurück zu Steffens Homepage
Zurück zur Mühlenseite
Vor zur Sägemühle
Vor zur Ölmühle
Vor zur Hammermühle
Weiter zu anderen Wassergetriebenen Werken
Vor zu historische Getreidemühlen